Woven bags have become a popular choice for packaging and transporting goods due to their durability, versatility, and eco-friendly nature. These bags are widely used in industries such as agriculture, retail, and construction, offering a strong and reliable option for storing various materials. But how exactly are woven bags made? In this comprehensive guide, we’ll take you through the entire manufacturing process, from selecting the raw materials to the final touches that make these bags ready for use.
Understanding Woven Bags
Before diving into the manufacturing process, it’s essential to understand what woven bags are and why they are so valuable. Woven bags are made by weaving strips of fabric, typically polypropylene (PP) or high-density polyethylene (HDPE), into a durable and flexible material. This woven structure gives the bags their signature strength, allowing them to hold heavy items without tearing.
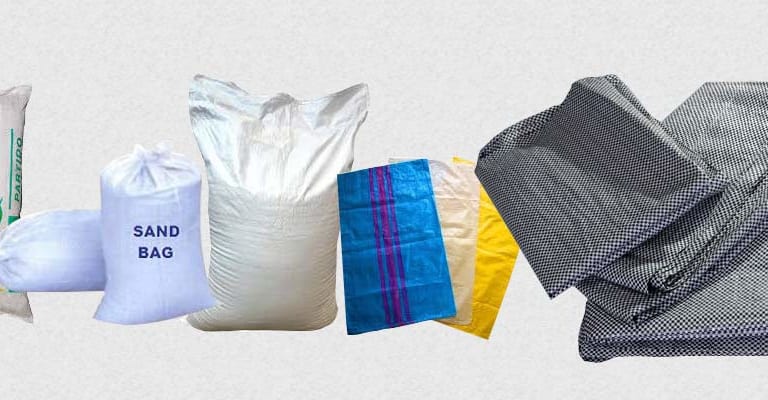
Woven bags are often used as packaging solutions for products such as grains, seeds, fertilizers, chemicals, and construction materials. Their resistance to wear and tear, along with the ability to be customized for branding, makes them a preferred choice for many industries.
Step 1: Raw Material Selection
The manufacturing process of woven bags begins with selecting the right raw materials. Polypropylene (PP) is the most commonly used material due to its strength, flexibility, and resistance to moisture. It is also lightweight, making it easy to transport. Polypropylene granules are used as the starting point, which will eventually be transformed into the woven fabric that forms the bags.
What Is Polypropylene?
Polypropylene is a thermoplastic polymer that is known for its high melting point, durability, and chemical resistance. It is widely used in various applications, from packaging materials to automotive parts. In the case of woven bags, its ability to be drawn into thin, strong threads makes it ideal for the weaving process.
Step 2: Extrusion and Tape Stretching
Once the raw polypropylene granules are selected, they undergo an extrusion process. During this stage, the granules are melted at a high temperature and then passed through a die to form a thin, continuous film. This film is then cut into narrow strips, which are known as tapes.
Stretching the Tapes
The tapes are stretched to increase their tensile strength, making them stronger and more durable. This stretching process helps to align the polymer molecules, which enhances the overall strength of the tapes. The stretched tapes are then wound onto spools, ready to be woven into fabric.
Step 3: Weaving the Fabric
The next step in the manufacturing process is weaving. The polypropylene tapes are fed into a circular weaving loom, which interlaces them to form a woven fabric. This woven structure is what gives the bags their strength and flexibility, allowing them to hold heavy items without tearing.
Circular Weaving Looms
Circular weaving looms are specifically designed to create tubular fabric, which can be cut and sewn into the desired shape of the woven bags. The weaving process ensures that the tapes are tightly interlaced, creating a durable material that can withstand the pressures of packaging and transportation.
Step 4: Lamination (Optional)
In some cases, woven bags require an additional layer of protection against moisture and other environmental factors. This is where lamination comes into play. During the lamination process, a thin layer of polypropylene film is applied to the woven fabric, providing a waterproof barrier that makes the bags suitable for storing moisture-sensitive items like grains and seeds.
Why Lamination Is Important
Lamination not only helps to protect the contents of the bags but also enhances the overall appearance of the bags by giving them a smooth surface. This smooth surface makes it easier to print logos and branding information, making laminated woven bags a popular choice for businesses looking to promote their brand.
Step 5: Cutting the Fabric
Once the woven fabric is ready, it is cut into the desired sizes to create individual bags. Cutting machines are used to ensure precise dimensions, allowing the bags to meet specific requirements. This step is crucial because the size and shape of the bags determine their capacity and suitability for different applications.
Cutting Techniques
There are various cutting techniques used in the industry, including hot cutting, which uses heat to seal the edges of the fabric, preventing fraying. This technique is particularly useful for creating a clean and professional finish, ensuring that the bags remain intact during use.
Step 6: Printing and Branding
With the fabric cut to size, the next step is to print any logos, brand names, or other information onto the bags. Printing can be done using different methods, such as flexographic printing or screen printing, depending on the complexity of the design and the desired finish.
Flexographic Printing
Flexographic printing is a popular method for printing on woven bags because it allows for high-quality images and text to be printed directly onto the fabric. It is a fast and efficient process, making it ideal for large production runs. This step helps businesses create customized bags that represent their brand, making the packaging not only functional but also a marketing tool.
Step 7: Sewing and Assembly
Once the printing is complete, the bags are ready to be sewn. The cut pieces of woven fabric are sewn together to form the final bag shape, with reinforced stitching at the seams for added strength. The bottom of the bag is typically double-stitched or folded and stitched to ensure that it can hold the weight of the contents without breaking.
Adding Handles or Liners
At this stage, additional features like handles or liners may be added to the bags. Handles can make the bags easier to carry, while liners can provide extra protection for the contents, such as moisture barriers for food-grade packaging.
Step 8: Quality Control
Quality control is a vital part of the manufacturing process to ensure that each woven bag meets industry standards. During this step, bags are checked for defects such as loose threads, inconsistent weaving, or printing errors. Bags that do not meet the required quality standards are removed from the batch to ensure that only the best products reach the customers.
Testing for Strength and Durability
In addition to visual inspections, some bags undergo stress tests to verify their strength and durability. These tests ensure that the bags can handle the weight of their intended contents without tearing or breaking.
Step 9: Packaging and Distribution
The final step in the production process is packaging and distributing the woven bags. The finished bags are neatly stacked and packed into bundles, ready to be shipped to distributors, retailers, or directly to businesses that need them for their packaging needs.
Ready for Market
Once the woven bags are packaged, they are ready to be distributed to various industries. These bags are then used for a wide range of applications, from storing agricultural products to packaging building materials and retail goods.
The Future of Woven Bag Manufacturing
As industries increasingly prioritize sustainability, the future of woven bag manufacturing is looking toward more eco-friendly practices. This includes using biodegradable materials, improving recycling processes, and finding ways to make the production process more energy-efficient. As demand for sustainable packaging solutions grows, woven bags continue to be a versatile and environmentally responsible choice.
Conclusion
Woven bags play a crucial role in packaging and transporting goods across various industries. From the careful selection of raw materials to the precision of cutting and sewing, each step in the manufacturing process ensures that these bags are strong, durable, and ready for use. Understanding how woven bags are made not only helps consumers appreciate their value but also highlights the efforts of manufacturers in providing reliable and eco-friendly packaging solutions. Whether you’re a business owner looking for a branding solution or a consumer interested in sustainable packaging, woven bags offer a practical and versatile option.